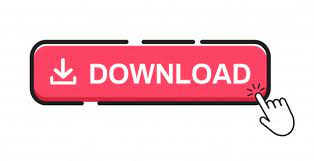
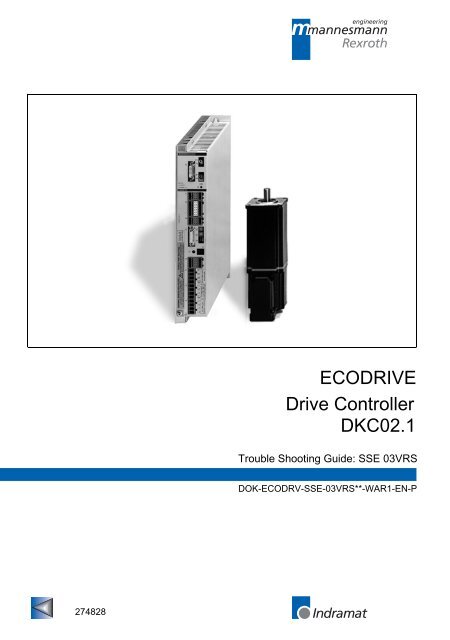
Battery life is limited, and capacity is also affected by temperature. The monitoring system can detect the abnormal condition of tire pressure only with high resolution. By detecting the change, the tire pressure is known.Īlthough this type of technology does not need battery power, it requires transponders to be integrated into tires, requiring common standards from tire manufacturers. When the surface acoustic wave reaches the surface of the piezoelectric substrate materials, there will be changes. The sensor of the passive tire pressure monitoring system is designed by a surface acoustic wave, and it produces a surface acoustic wave through a radio frequency electric field. But its disadvantage is also prominent, whose induction module needs battery power, so there is a problem of service life. The active system is a relatively mature technology, and the developed module can be applied to the tires of various brands.
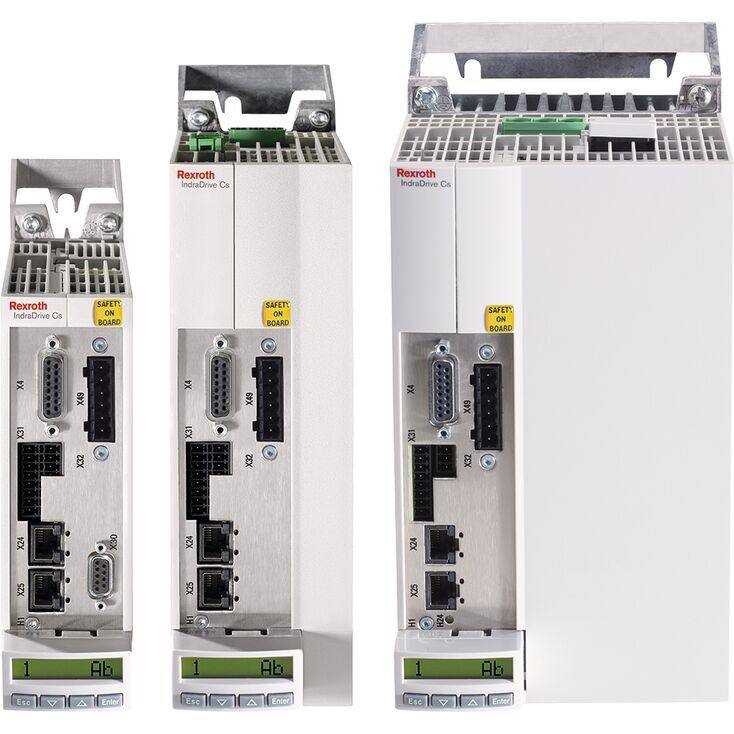
Then the wireless receiver installed in the cab receives the pressure sensor signals, after a certain signal processing, and shows the tire pressure. The pressure sensor is installed on each wheel rim, transmitting a radio frequency signal. The active system is achieved by using mems technology on silicon capacitive or piezoresistive pressure sensors. The direct tire pressure monitoring system is divided into two types that are active and passive. The factors such as speed and detection accuracy cannot be taken into account simultaneously. It can not alarm when the pressure of the same axle or wheel on the same side or all tires drop at the same time. The exact instantaneous pressure of each tire cannot be displayed. And the main disadvantages lie in the following three aspects. When the pressure is too low, the system will automatically alarm.Īs for the indirect tire pressure monitoring system, the wheel speed sensor of the automobile ABS system compares the speed difference between tires, so as to achieve the purpose of monitoring tire pressure. Tire pressure monitoring system (TPMS) mainly has two kinds of solutions, direct system and indirect system.Ī direct tire pressure monitoring system is the use of pressure sensors installed in each tire to directly measure the tire pressure, and display and monitor it.

When the tire pressure reached a reasonable value, it can improve safety, but also can save fuel consumption, according to the relevant data statistics. Advanced manufacturing and process technology strengthen the performance of sensors, and tire pressure monitoring is increasingly accurate.Īt present, in order to ensure the safety of driving, most car tires are equipped with pressure sensors to detect pressure change. The development of the automotive industry stimulates the improvement of automotive pressure sensors. “The Evolution I coder is just far more convenient, far cleaner, and far more consistent,” Piper concludes.Figure 1: The tire pressure monitoring system.Īutomotive sensors are the fastest growing and most used type in recent years. The case-coder is capable of operating at 425 pieces/hr on Line 1, and at 360/hr on Line 3. Piper adds that printer programming is easy too, through the use of a hand-held controller that connects to a USB port. While Piper notes that the cartridges themselves cost more than the consumables used before, “that’s offset by the reliability and the lack of cleanup required,” he declares.
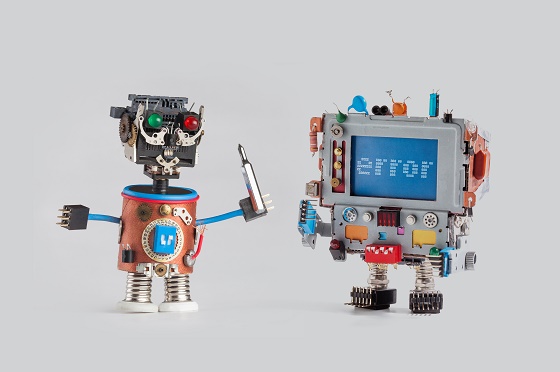
The Evolution I high-resolution, large-character ink-jet printer, supplied by Associated Packaging ( uses Hewlett-Packard ink-cartridge technology. Then on Line 1, there were times when the old equipment simply wouldn’t reset properly, so you would end up with a case that didn’t have a date code, and you would have to go back and hand-stamp it anyway.” The Folsom, CA, facility replaced the contact-style roller coding system and hand-stamping operations on its first and third package-filling lines, respectively, with Evolution I printers to ensure consistent and reliable date-coding.Ĭiting the challenges of Gekkeikan’s previous coding solutions, vice president of production Bill Piper says, “First of all, you have the messiness of dealing with ink. is saying sayonara to messy, unreliable date coding for its corrugated cases of sake product with new high-resolution ink-jet printers from Digital Design ( ).
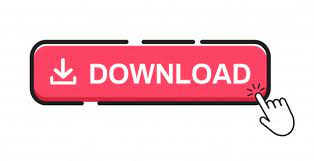